As the packaging industry converges at Drupa 2024, a true game-changer awaits in the Landa Digital Printing booth – the anticipated W11 Nanographic printing® capabilities demonstration. This soon-to-be-launched digital printing solution is poised to elevate flexible packaging with unparalleled print quality, productivity, and sustainable manufacturing capabilities. In Dusseldorf, Landa showcases printed mainstream packaging solutions, manufactured in collaboration with Plastopil Group companies providing various flexible mono-material films. All are fully recyclable in the common recycling streams.
Pushing Boundaries in Sustainable Mono-Material Packaging
The first product showcased is a folded gusset stand-up pouch constructed entirely from mono-material polyethylene. Manufactured by Karlville Swiss, this 100-micron zipper pouch utilizes Polysack’s recyclable Pack N Cycle LC 25 MDO PE film as the base material. Landa’s W11 Nanographic printing press was employed to perform reverse printing on this PE film, which was subsequently laminated with a PE film from MOR Industries to create a mono-PE structure.
This packaging solution offers excellent moisture barrier properties with a low water vapor transmission rate (WVTR). Importantly, this pouch can be recycled through conventional PE recycling streams by eliminating multi-material laminates, promoting a circular economy approach. Its applications include packaging nuts, berries, sweets, and similar products.
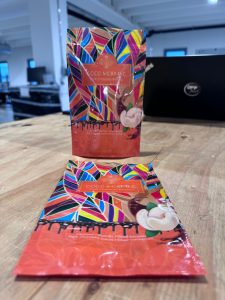
Printed Sample of Mono PE Gusset Folded Stand-Up Pouch, presented at Drupa 2024, W11 zone, Landa booth.
The second product is a mono-material PP packaging solution for chilled food such as sliced meat, cheese, and similar applications. The packaging bottom web is a 200-micron thermoforming mono-PP from Plastopil’s Multiform SUS portfolio. The 60-micron top lid features a 20-micron BOPP layer printed by the Landa W11 and laminated to Plastopil’s 38-micron, 9-layer high-barrier PP film. This complete mono-PP packaging solution eliminates multi-material laminates, is microwave-safe and can endure sterilization up to 95°C.
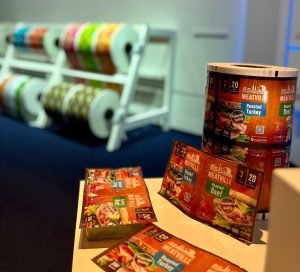
Printed Samples of Mono-PP Thermoformed Packaging Solution
Sustainable, Solvent-Free Production
All lamination processes performed by Plastopil were 100% solvent-free, underscoring Plastopil and Landa’s commitment to environmentally conscious manufacturing. The films were processed on standard packaging machines and performed well. The sustainability benefits are considerable – truly circular packaging using less plastic without sacrificing performance.
Drupa 2024 provides a comprehensive look at the future of sustainable flexible packaging. In addition to the printed pouches, Landa’s booth showcases printed slit and jumbo rolls produced via this partnership.
This collaboration highlights Plastopil Group’s focus on innovation and sustainability. Polysack is a prominent manufacturer and pioneer in ready-to-recycle, mono-oriented PE (MOPE) films, while MOR Industries specializes in incorporating recycled materials and producing mono-material film solutions.
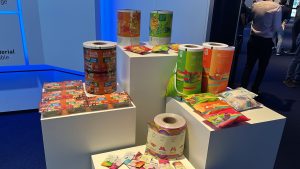
Landa and Plastopil group collaboration present: printed slit and jumbo rolls at Drupa 2024, W11 zone, Landa booth.
If you’re interested in learning more about our flexible packaging solutions, with all the advantages and benefits of dry food packaging, contact us for additional information.